Warehouse safety using computer vision is redefining risk management in today’s high-speed logistics operations. As traditional methods like signs and manual checks fall short, AI-powered visual monitoring offers a proactive approach to identifying hazards before they lead to accidents. In this guide, we’ll explore how intelligent camera systems not only boost safety but also streamline workflows for modern warehouse leaders aiming for smarter, safer operations.
Understanding Warehouse Safety using Computer Vision
What is Computer Vision in Warehouse Safety?
Computer vision in warehouse safety refers to the use of AI-powered visual systems to proactively detect and respond to hazards in high-risk logistics environments. Unlike conventional CCTV systems that simply record activity, computer vision platforms continuously analyze footage to identify safety threats such as blocked emergency exits, unauthorized personnel in restricted zones, or unsafe forklift behavior.
Through advanced deep learning models and real-time data interpretation, these systems act as tireless safety supervisors, spotting hazards before they turn into accidents. For example, if a pallet is improperly stacked near a walkway or a forklift approaches a pedestrian crossing at an unsafe speed, the system can trigger instant alerts. By transforming passive surveillance into active protection, computer vision enables warehouses to maintain high safety standards with greater consistency and efficiency.
How Computer Vision Transforms Traditional Safety Methods
Traditional warehouse safety relies heavily on manual observation, sporadic audits, and post-incident investigations—methods that often fall short of preventing accidents. Computer vision fundamentally transforms this approach by providing continuous, real-time alerts and comprehensive coverage of warehouse environments. The technology shifts safety management from reactive to predictive, enabling automated inspection capabilities that identify risks before they materialize into incidents.
The transformation is particularly evident in hazard identification processes. Where human supervisors might miss subtle safety violations due to blind spots, fatigue, or divided attention, computer vision systems maintain unwavering focus across multiple areas simultaneously. This technological evolution enables warehouses to achieve unprecedented visibility into their safety landscape, creating what industry experts describe as a “synergistic safety ecosystem”.
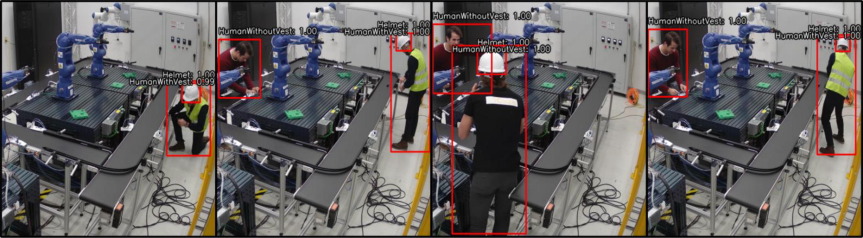
Key Components of Vision AI Safety Systems
Modern computer vision safety systems integrate several critical components to deliver comprehensive worker safety protection. The foundation consists of high-resolution cameras strategically positioned throughout warehouse facilities, connected to powerful processing units capable of real-time analysis. These systems leverage models like YOLO11, which excel at object detection and instance segmentation tasks essential for identifying obstacles, equipment, and personnel in dynamic warehouse environments.
The AI infrastructure includes sophisticated algorithms trained on extensive datasets of warehouse scenarios, enabling accurate recognition of safety equipment, dangerous behaviors, and environmental hazards. Integration capabilities allow these systems to connect with existing warehouse management systems, creating seamless workflows that enhance rather than disrupt current operations. Cloud-based processing options provide scalability while reducing upfront infrastructure costs, making advanced safety technology accessible to warehouses of all sizes.
Critical Safety Applications of Computer Vision in Warehouses
The application of computer vision in warehouse safety spans multiple use cases, ranging from equipment monitoring to behavioral analytics. Below are the most impactful implementations currently transforming logistics operations.
Forklift Zone Monitoring and Collision Prevention
Forklift operations represent one of the most significant safety challenges in warehouse environments, making collision prevention a critical priority for safety compliance initiatives. Computer vision systems establish virtual safety zones around forklift operations, continuously monitoring equipment movements and triggering immediate alerts when these heavy machines enter restricted areas or operate in unauthorized ways. This proactive approach prevents collisions before they occur while ensuring proper traffic flow throughout facilities.
The technology employs sophisticated object tracking capabilities that continuously monitor forklift movements in real-time, analyzing movement patterns and predicting trajectories to identify potential collision risks. Unlike simple object detection that identifies objects in single frames, advanced tracking follows equipment across multiple frames, enabling systems to understand how forklifts interact with their environment and anticipate dangerous situations before they develop.
Machine vision systems can detect when forklifts approach blind corners, enter pedestrian zones, or operate too close to storage racks, immediately alerting operators and supervisors to take corrective action. This level of monitoring significantly reduces the risk of the thousands of forklift-related injuries reported annually while improving overall warehouse traffic management.
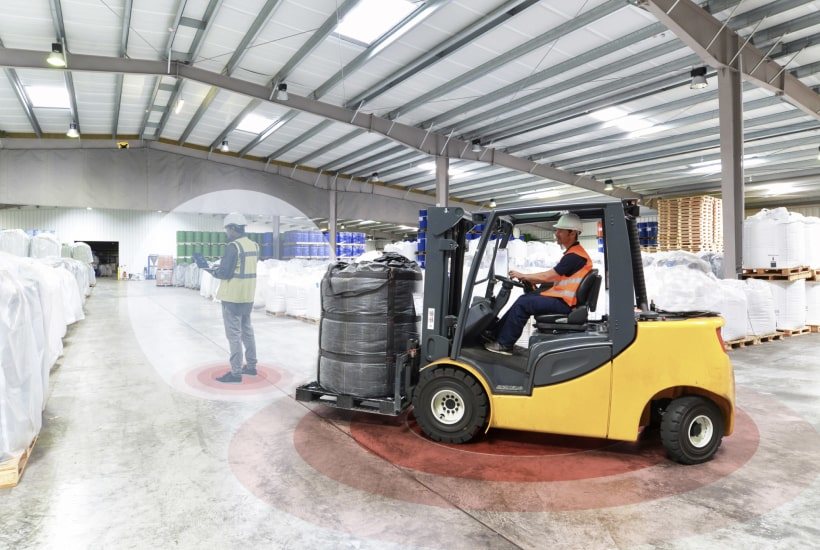
PPE Compliance Detection and Monitoring
Personal Protective Equipment compliance monitoring represents another critical application where computer vision delivers substantial safety improvements. According to OSHA, PPE compliance failures rank among the top safety violations, yet traditional monitoring methods rely heavily on human supervision that can miss violations due to oversight or limited coverage. Computer vision systems provide continuous automated inspection of PPE compliance, immediately identifying when workers are missing required safety gear such as helmets, high-visibility vests, or safety glasses.
The technology analyzes visual data to verify proper PPE usage across entire warehouse facilities, maintaining compliance without requiring supervisors to conduct constant manual checks. Advanced systems can distinguish between different types of protective equipment and verify correct usage, ensuring workers receive appropriate protection for their specific work environments. This comprehensive monitoring approach helps warehouses maintain regulatory compliance while protecting workers from preventable injuries.
Unsafe behavior detection capabilities extend beyond simple PPE verification to identify improper equipment usage, dangerous lifting techniques, or workers entering hazardous areas without appropriate protection. These systems create detailed compliance reports that help management identify training needs and implement targeted safety improvements.
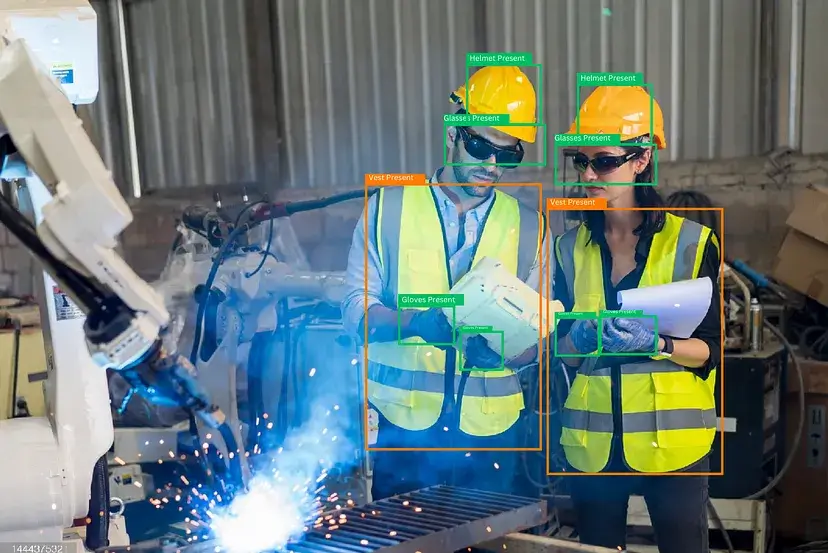
Restricted Zone Surveillance and Access Control
Warehouse facilities often contain areas with heightened safety risks due to dangerous machinery, hazardous materials, or specialized operations requiring restricted access. Computer vision systems excel at establishing virtual boundaries around these zones, automatically detecting unauthorized entry and alerting security personnel to potential violations. This technology creates invisible safety perimeters that adapt to changing warehouse configurations without requiring physical barriers or constant human monitoring.
The surveillance capabilities extend to monitoring emergency exits and safety pathways, ensuring these critical routes remain clear and accessible. When obstructions like improperly stored equipment or personnel gatherings are detected, systems immediately alert staff to take corrective action, helping organizations maintain compliance with safety regulations while reducing risks during emergencies.
Environment monitoring features can detect environmental hazards such as liquid spills that could cause slips or equipment skidding. By analyzing surface reflections and textures, these systems distinguish between safe and hazardous floor conditions, enabling rapid response to prevent accidents before workers encounter dangerous areas.
Fall Detection and Emergency Response
Advanced computer vision systems incorporate sophisticated fall detection algorithms that can identify when workers experience accidents or medical emergencies. These systems analyze movement patterns and body positions to detect sudden falls, unusual postures, or signs of distress, immediately triggering emergency response protocols. The technology provides crucial incident reduction capabilities by ensuring rapid response to workplace emergencies.
Integration with IoT sensors and wearable devices enhances fall detection accuracy while providing additional health monitoring capabilities. Systems can detect signs of worker fatigue, overheating, or other health issues that might lead to accidents, enabling proactive intervention before emergencies occur. This comprehensive approach to worker monitoring creates multiple layers of protection that significantly improve emergency response times and outcomes.
The Computer Vision Safety Implementation Process
System Setup and Camera Installation
Successful computer vision implementation begins with computer vision camera placement that maximizes coverage while minimizing blind spots throughout warehouse facilities. Professional installation teams conduct comprehensive site surveys to identify optimal camera positions that provide clear sightlines to critical areas including forklift zones, pedestrian pathways, loading docks, and restricted areas. High-resolution cameras with appropriate lighting capabilities ensure clear image capture under varying warehouse conditions.
Network infrastructure requirements include high-speed internet connectivity and robust data processing capabilities to handle real-time video analysis. Modern systems often leverage edge computing to process data locally, reducing latency and improving response times for critical safety alerts. Cloud integration provides scalability and remote monitoring capabilities while ensuring data security and system reliability.
AI Model Training and Calibration
Effective computer vision systems require extensive training on warehouse-specific scenarios to achieve accurate hazard identification and minimize false alerts. Training datasets must include diverse examples of normal operations, safety violations, equipment types, and environmental conditions specific to each warehouse environment. Machine learning algorithms continuously improve their accuracy through operational feedback, adapting to unique warehouse characteristics and operational patterns.
Calibration processes involve fine-tuning detection thresholds, establishing appropriate alert sensitivity levels, and configuring response protocols for different types of safety events. This customization ensures systems provide actionable alerts without overwhelming operators with false positives that could reduce system effectiveness.
Integration with Existing Safety Systems
Modern computer vision platforms are designed to integrate seamlessly with existing warehouse management systems, safety protocols, and emergency response procedures. API connections enable data sharing between vision systems and warehouse management software, creating comprehensive safety dashboards that provide real-time visibility into all safety metrics and incidents.
Integration capabilities extend to connecting with alarm systems, emergency lighting, and communication networks to ensure coordinated responses to safety events. This holistic approach creates unified safety ecosystems where computer vision enhances rather than replaces existing safety infrastructure.
Benefits and Challenges of Computer Vision Warehouse Safety
Benefits of Computer Vision Warehouse Safety
Computer vision technology delivers transformative benefits that extend far beyond traditional safety monitoring capabilities. Real-time alerts enable immediate response to safety violations, significantly reducing the time between hazard identification and corrective action. This rapid response capability can prevent minor safety issues from escalating into serious accidents, creating substantial improvements in overall warehouse safety performance.
Cost reduction represents another significant advantage, as automated monitoring reduces the need for constant human supervision while improving safety coverage. Warehouses can achieve comprehensive safety monitoring with fewer personnel dedicated to safety oversight, allowing staff to focus on higher-value activities while maintaining superior safety standards. The technology also provides detailed documentation of safety events and compliance metrics, supporting regulatory reporting requirements and insurance considerations.
Operational efficiency improvements emerge as computer vision systems optimize traffic flow, reduce equipment downtime due to accidents, and minimize disruptions caused by safety incidents. Inventory security benefits include theft detection and unauthorized access monitoring, protecting valuable warehouse assets while maintaining safety standards.
Challenges of Computer Vision Warehouse Safety
Implementation challenges include the technology’s relative novelty, which may lead to initial system bugs or integration issues that require technical resolution. Success depends heavily on data quality and structure, requiring extensive, accurately labeled training datasets to achieve optimal performance. Environmental factors such as lighting variations, dust, and equipment configurations can affect system accuracy, necessitating ongoing calibration and maintenance.
Initial investment costs for high-quality cameras and processing infrastructure can be substantial, though reduced insurance costs and improved operational efficiency typically offset these expenses. Organizations must also invest time and resources in staff training to ensure effective system utilization and maintenance. Technical expertise requirements may necessitate partnerships with specialized vendors or internal capability development to maximize system effectiveness.
Future Trends in Computer Vision Warehouse Safety
The future of computer vision warehouse safety will be shaped by integration with IoT sensors, 5G connectivity, and advanced predictive analytics capabilities. IoT networks will enable comprehensive device communication, allowing forklifts, robots, and inventory systems to share real-time status information that enhances safety monitoring accuracy. 5G connectivity will support more sophisticated real-time processing and enable advanced features like augmented reality safety training and remote expert assistance.
Predictive analytics represent the next frontier in warehouse safety, with systems that will identify subtle precursors to accidents that human observers might miss. Future platforms will incorporate comprehensive risk modeling that creates dynamic safety assessments based on multiple variables including weather conditions, equipment status, worker fatigue levels, and operational intensity. Automated intervention capabilities will enable systems to initiate preventive measures automatically when risk levels exceed predetermined thresholds.
Edge AI processing, 3D vision systems, and deep learning-based anomaly detection will enable even more precise monitoring and predictive capabilities. Autonomous robots and drones equipped with computer vision will perform real-time safety audits, automated hazard identification, and intelligent space optimization. Integration with digital twin technology will create fully connected, self-optimizing warehouse environments that continuously improve safety performance through machine learning and operational feedback.
Conclusion
Computer vision technology represents a fundamental transformation in warehouse safety management, shifting from reactive incident response to proactive accident prevention and comprehensive risk assessment. The technology’s ability to provide continuous visual monitoring, immediate hazard detection, and intelligent automated inspection capabilities creates unprecedented opportunities for improving worker safety while enhancing operational efficiency.
Stay updated with the latest in computer vision technology—explore more insights and innovations with us today.