Defect detection with computer vision has revolutionized manufacturing quality control, enabling companies to achieve accuracy rates exceeding 99% while processing thousands of products per minute. Traditional manual inspection methods struggle with consistency and speed, but computer vision defect detection systems can identify microscopic flaws that human inspectors often miss. Advanced AI-powered defect detection solutions are transforming how manufacturers approach quality assurance, delivering unprecedented precision in automated defect detection processes. Discover how defect detection with computer vision is reshaping manufacturing standards and driving operational excellence across industries.
What is Defect Detection?
Defect detection functions as a comprehensive framework for locating anomalies, product imperfections, or quality specification deviations within manufactured components. This critical quality control measure encompasses various types of imperfections, from surface scratches and dimensional inaccuracies to missing components and assembly errors.
Conventional manual inspection approaches depend extensively on human assessment capabilities, creating inherent inconsistencies and operational constraints. Human inspectors can become fatigued, may miss minute details, and often apply subjective criteria when evaluating product quality. These can affect the quality of the final product, leading to significant losses from product recalls and damage to brand reputation.
Modern fault identification systems address these challenges by implementing consistent, objective criteria for quality assessment. Computer vision technology can detect defects as small as 0.1mm, far beyond human visual capabilities. This precision is particularly crucial in industries like electronics manufacturing, where microscopic soldering defects can cause complete system failures.
Read more: Defect Detection with AI: The Secret to Smart Quality Control
Why Is Computer Vision Used for Defect Detection?
The adoption of machine learning and computer vision for defect detection stems from several compelling advantages over traditional inspection methods. Real-time processing capabilities allow manufacturers to identify and address quality issues immediately, preventing defective products from progressing through the production line.
Manufacturing efficiency improves dramatically when computer vision systems are implemented. Unlike human inspectors who require breaks and can only work limited hours, AI systems for defect classification operate continuously, maintaining consistent performance 24/7. This continuous operation is essential for modern production environments that demand high throughput and minimal downtime.
Advanced sensor technology integrated with computer vision systems delivers exceptional precision in anomaly detection processes. Modern high-resolution cameras and specialized imaging components capture detailed visual data across multiple spectral ranges – from infrared thermal imaging to ultraviolet light detection. These capabilities reveal manufacturing defects that remain completely invisible to human inspectors. Multi-spectral detection is particularly valuable in detecting internal structural defects or material inconsistencies.
Cost-effectiveness represents a compelling advantage of computer vision defect detection systems. While initial implementation requires substantial investment, the long-term financial benefits prove remarkable. According to industry reports, a leading consumer goods manufacturer achieved annual savings exceeding $500 million after deploying computer vision technology across their dental hygiene production lines. These savings resulted from reduced product recalls, decreased manual inspection costs, and improved production efficiency.
What Do You Need for Defect Detection with Computer Vision?
Implementing effective AI for visual quality control in production requires several key components working in harmony. The foundation begins with high-quality image analysis hardware, including industrial-grade cameras capable of capturing high-resolution images at production-line speeds.
Lighting systems play a crucial role in successful defect detection. Proper illumination ensures consistent image quality regardless of environmental conditions or product variations. LED lighting arrays, often combined with specialized filters, create optimal conditions for visual defect inspection.
Processing power is essential for real-time defect detection using computer vision. Modern systems typically employ edge computing devices or dedicated GPU clusters to handle the intensive computational requirements of deep learning in defect detection for manufacturing. These systems must process multiple high-resolution images per second while running complex AI algorithms.
The software component requires sophisticated machine learning for defect detection algorithms. Pre-trained models can be customized for specific applications, or companies can develop custom models using frameworks like TensorFlow or PyTorch. The choice depends on the specific defect types, product characteristics, and accuracy requirements.
Training data is arguably the most critical requirement. To successfully deploy the system, a dataset may need to include thousands of labeled images showing both standard and defective products. The dataset must be comprehensive, covering all possible defect types and variations that may occur during the production process.
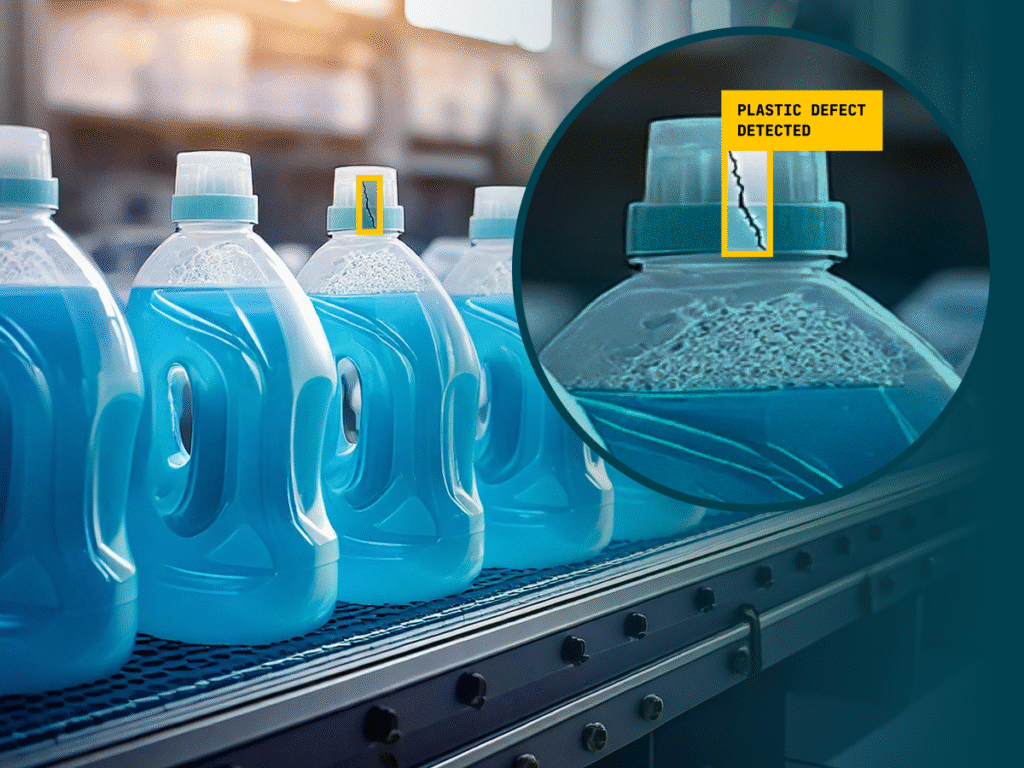
How the Process Works: 5 Key Steps
Step 1: Data Acquisition
The defect detection process begins with systematic image analysis through high-resolution cameras strategically positioned along the production line. These cameras capture detailed images of products at predetermined intervals, ensuring complete coverage of all critical surfaces and components.
Modern sensor technology enables capture rates of up to 1000 frames per second, allowing inspection of products moving at high speeds without compromising image quality. Multiple cameras may be positioned at different angles to provide comprehensive 360-degree coverage of complex products.
Synchronization systems ensure that image capture occurs at precisely the right moment, accounting for product movement and positioning. This timing precision is crucial for maintaining consistent image quality and ensuring that all products receive a thorough inspection.
Step 2: Data Preprocessing
Raw images undergo sophisticated preprocessing to enhance features relevant to defect detection. This stage involves noise reduction, contrast enhancement, and edge detection algorithms that highlight potential defect areas. Automation in this preprocessing stage ensures consistent image quality regardless of lighting variations or environmental conditions.
Color normalization and geometric correction compensate for minor variations in camera positioning or lighting conditions. These adjustments ensure that the AI model receives standardized input data, improving detection accuracy and reducing false positives.
Advanced preprocessing techniques may include multi-spectral analysis, where images captured in different light spectrums are combined to reveal defects not visible in standard visible light imaging.
Step 3: The AI Model in Action
The preprocessed images are analyzed by sophisticated deep learning in defect detection for manufacturing algorithms. Convolutional Neural Networks (CNNs) examine the images pixel by pixel, comparing observed patterns against learned defect signatures.
Machine learning for defect detection models have been trained on extensive datasets containing thousands of examples of both defective and acceptable products. This training enables the system to recognize subtle patterns and anomalies that indicate various types of defects.
The AI model assigns confidence scores to detected anomalies, allowing for fine-tuned sensitivity adjustments based on specific quality requirements. This scoring system enables manufacturers to balance detection sensitivity with production throughput.
Step 4: Decision & Output
Based on the AI analysis, the system makes real-time decisions about product quality. Products exceeding defect thresholds are automatically flagged for removal from the production line. This real-time processing capability prevents defective products from progressing to subsequent manufacturing stages.
The system generates detailed reports documenting defect types, locations, and severity levels. This data provides valuable insights for process improvement and quality trend analysis. Quality control managers can use this information to identify recurring issues and implement preventive measures.
Alert systems notify operators immediately when defects are detected, enabling rapid response and minimizing production disruptions. Integration with manufacturing execution systems (MES) ensures that quality data is incorporated into overall production management.
Step 5: Integration & Feedback
The final step involves seamless integration with existing automation systems and continuous learning mechanisms. Defect detection results are fed back into the AI model to improve future performance through ongoing training.
Integration with robotic systems enables the automatic removal of defective products without human intervention. This manufacturing efficiency improvement reduces labor costs and eliminates the risk of human error in the rejection process.
Continuous monitoring and model updates ensure that the system adapts to new defect types or changes in product specifications. This adaptive capability maintains high detection accuracy over time.
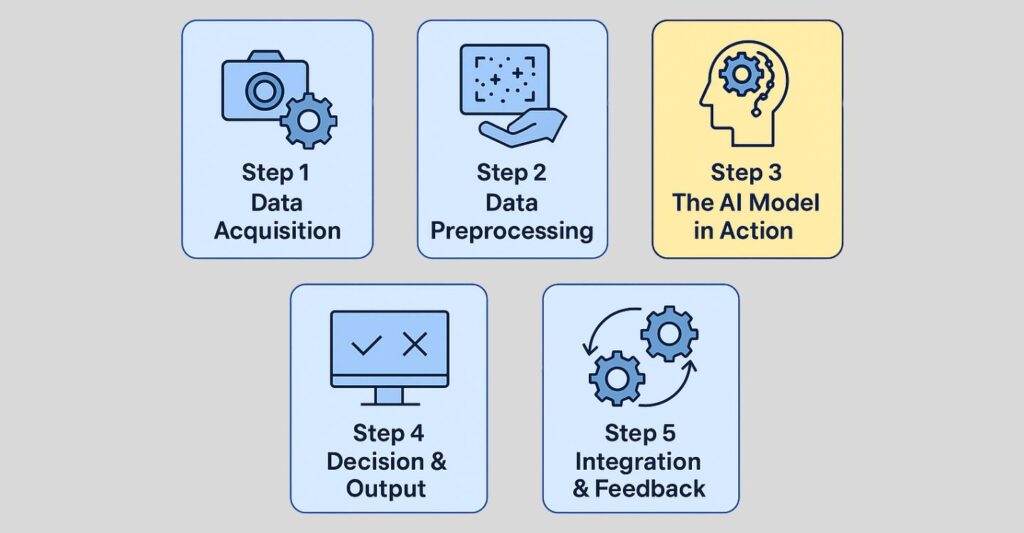
Defect Detection in the Real World: Examples by Industry
Automotive Industry
Computer vision systems analyze vehicle components to detect surface flaws, positioning errors, and finish quality variations. These systems can detect microscopic scratches on painted surfaces and ensure that safety-critical components meet stringent quality standards. Advanced systems examine weld quality in structural components, identifying potential failure points before they compromise vehicle safety.
Electronics Manufacturing
AI systems for defect classification inspect printed circuit boards (PCBs) for soldering defects, component misplacements, and surface anomalies. The precision required in electronics manufacturing makes computer vision essential, as defects measured in micrometers can cause complete system failures. These systems can identify missing components, incorrect orientations, and solder joint quality issues with remarkable accuracy.
Also read: AI in manufacturing: 10 Practical Applications and Examples
Food and Beverage
In food processing, computer vision detects foreign objects, packaging defects, and labeling issues while ensuring compliance with food safety regulations. Systems can identify contamination, verify fill levels in containers, and check label placement and print quality. This application is particularly critical given the health implications of defective food products.
Textiles and Apparel
Visual defect inspection systems identify fabric defects such as tears, stains, color mismatches, and weaving irregularities. These systems help maintain quality standards in clothing manufacturing while reducing waste production through early defect detection.
Aerospace
The aerospace industry employs computer vision for critical safety inspections, detecting surface cracks, corrosion, and structural defects that could compromise aircraft safety. These systems must meet extremely high accuracy standards given the safety-critical nature of aerospace applications.
Challenges in Defect Detection with Computer Vision
Despite its advantages, implementing computer vision for visual defect inspection presents several challenges that manufacturers must address.
Lighting conditions
Lighting conditions represent a primary concern, as variations in illumination can significantly impact detection accuracy. Consistent, high-quality lighting systems are essential but can be expensive to implement and maintain.
Anomaly detection complexity
Anomaly detection complexity increases with product variety and defect types. Training AI models to recognize all possible defect variations requires extensive datasets and significant computational resources. Some defect types may be rare, making it difficult to collect sufficient training examples.
Environmental factors
Ambient conditions such as airborne debris, equipment oscillations, and temperature instability can impact computer vision system reliability. Production environments generate harsh operational circumstances that potentially degrade camera operations and image capture quality. Reinforced system construction and routine servicing schedules remain critical for ensuring consistent operational effectiveness.
Integration with existing production systems
Integration with existing production systems can be complex and costly. Legacy manufacturing equipment may require significant modifications to accommodate computer vision systems. This integration challenge often requires careful planning and phased implementation approaches.
False positive and false negative rates
False positive and false negative rates must be carefully balanced. Overly sensitive systems may flag acceptable products as defective, reducing throughput and increasing costs. Conversely, systems that miss actual defects can allow faulty products to reach customers, potentially causing safety issues and brand damage.
Conclusion
Computer vision defect detection represents a transformative technology that addresses the critical quality control challenges facing modern manufacturing. By implementing AI-powered defect detection in manufacturing, companies can achieve unprecedented accuracy levels while maintaining high production throughput and reducing operational costs.
At Sky Solution, we offer customized AI and Computer Vision services tailored to each business’s unique needs. If you’re looking for expert guidance, don’t hesitate to contact us today!